PVC管材塑化度判断
比较硬质PVC管材塑化度与力学性能的关系,得出硬质PVC管材塑化度的最佳范围为60%~70%。分析配方、混料、工艺条件对塑化度的影响,以指导生产过程,并将塑化度调整到最佳塑化范围。
在加工过程中,硬质PVC的粒子结构将发生很大变化,在较低加工温度下,由于热和剪切力的作用,颗粒分解成初级粒子;随着温度的升高,初级粒子部分被粉碎;当加工更高时,初级粒子可全部粉碎,晶体熔化,边界消失,形成二维网络,这一过程称为熔融或凝胶化,一般成为塑化。塑化度正是制品结晶程度与PVC初级粒子熔化程度的反映,塑化度可用流变法测量。
PVC塑化后在制品中形成了贯穿的结晶网络,这种结构的变化,必然引起力学性能的改变,进而影响制品的性能。因此,在硬质PVC加工过程中,控制好塑化度,使制品各部分塑化均一,对保证硬质PVC管材质量非常重要。国家技术监督局发布的GB/T10002.1-1996中,用增加二氯甲烷浸渍试验来反映管材塑化的情况。
1、硬质PVC管材的最佳塑化度
硬质PVC未塑化或塑化度低时,PVC初级粒子未解体或解体很少,粒子间还未融合;塑化度100%时,所有初级粒子融合,制品冷却后,可形成均匀分布,贯穿整个制品的结晶网络,晶网会限制分子链的运动。这两种结构的管材冲击强度较低,与管材韧性有关的指标(如落锤冲击性能)不易达标,这两种塑化度的管材都不是我们希望的。
大量研究和测试结果表明:硬质PVC管材的综合性能最佳值是在塑化度为60%~70%时得到的。因此,我们应选择适当的条件,使塑化度均匀并控制在此范围内。
2、塑化度的调整
塑化度的调整应从配方、混料、加工条件等方面综合考虑。
(1)PVC树脂
用悬浮法生产的PVC树脂有疏松型和紧密型。疏松型树脂表皮较薄、内部疏松、亚粉粒体积较大且大小均匀,易于破碎,释放初级粒子。这样的树脂经混合,可使助剂分布均匀,经过挤出加工后,易获得塑化均一的管材。
除PVC树脂的形态外,树脂的相对分子量也影响塑化,相同配方和加工条件下,分子量越大,虽然管材韧性好,但塑化度降低。
(2)稳定剂
目前,国内采用的主要热稳定剂为铅系稳定剂(主要为三碱式硫酸铅,硬脂酸铅等)。固体铅盐稳定剂分散性差,难塑化易造成大的应力集中,要求所用铅盐越细越好,最好经过研磨。另外,铅盐对人体健康有害,这些稳定剂在给水管配方中用量有限制,如含铅稳定剂用量不能超过3份。
(3)润滑剂
外润滑性强的配方使PVC受到较小的剪切力,低的剪切力水平可提高初级粒子“存活”的温度或延长其“寿命”,所以在相同的加工条件下,润滑性强的配方,可使管材塑化度降低。为了使管材塑化度保持一定,就要增加加工设备的剪切能力(如提高螺杆转速)或提高加工温度,或延长物料在设备中停留的时间(提高机台阻力既可延长“停留时间”,又可增加剪切强度)。
(4)改性剂对塑化的影响
使用抗冲击改性剂时,物料粘附金属倾向增强,剪切摩擦热增加,往往会促进塑化,故应适当增加润滑剂用量,以适当推迟塑化,获得最佳塑化度。
但选择CPE作改性剂时,相对分子量低的外润滑剂如石蜡易溶于CPE中,降低润滑效果,还会影响增韧效果,应选用与改性剂相容性差,相对分子量或熔点较高的润滑剂,如聚乙烯蜡、高级脂肪酸及其它皂类润滑剂。具有核——壳结构的改性剂,其极性很强的壳会阻碍润滑剂进入软芯,因此对润滑剂的选择不很严格。
3、混合的调整
混合是指降低组分料非均匀性的过程。因此,混料质量好坏将影响塑化是否均一。实际加工中遇到的许多问题,如挤出过程中混料脉动,塑化不均等均与混料有关。
硬质PVC管材混料多采用高速混合机进行,冷混机冷却。
混料中应注意以下问题:
(1)混合机加料量选择
物料体积为高速混合机空容积50%以下时,摩擦热小,达到混合温度(120℃)需15min以上;加料量50%~70%,达到混料温度仅为8min~10min;加料量在70%以上混合效果变差,物料的物性不均一,导致管材塑化不均。因此,我们应将加料量控制在混合室空容积的50%~70%。
(2)高速混合温度的选择
料温在50℃以下时,PVC树脂颗粒在强力搅拌下,其粉粒和亚粉粒被击碎,干粉料的表观密度变化不大。
料温在80℃以上到120℃左右时,树脂颗粒胀大,颗粒尺寸趋于均匀,颗粒的平均尺寸与原始状态相近,同时,干混料密度迅速增加。料温在120℃以上,树脂颗粒尺寸减少而干混料表观密度仍在提高。
树脂颗粒变大并均匀地在干粉料中流动,使输送量均匀,再考虑到100℃以上时对排出干燥物料中的水汽有益处,所以一般高速混合温度在100℃~120℃。
对于普通单螺杆挤出机,直接用粉料生产时,为了使管材有高的塑化度,往往将热混温度提高到140℃以上,但是不宜超过150℃。这是因为固体稳定剂仅粘附于树脂颗粒表面,对内部的PVC起不到稳定作用,热混温度太高会使树脂分解变色。而冷混温度在40℃左右即可。
(3)高速混合时的加料顺序
硬质PVC配方的加料顺序应有利于助剂作用的发挥,避免助剂的不良协同效应,并有利于提高分散程度和速度。
稳定剂与树脂同时加入到热混机中,以便及早发挥稳定作用。
皂类和内润滑剂随后加入,以便充分渗入树脂内部。蜡类外润滑剂宜在料温接近出料温度时再加,以免蜡类干扰其它助剂的分散。
填料对助剂有吸收作用,宜最后加入。以便助剂先在树脂中得以分散。
加工改性剂宜在蜡类加入之前,稳定剂加入之后加入,对于具有防止热分解倾向的改性剂,如CPE,可与树脂一并加入。如果考虑冲击改性剂吸收润滑剂的倾向强于PVC树脂,为避免润滑剂被吸收后物料加工性的明显变化,及吸收润滑剂后改性效果的降低,也可在最后加入。易结团的冲击改性剂,为了使其分散良好,宜最后加入。
总之,助剂的加料顺序应避免助剂间的相克相消,提高相辅相成的效果,使助剂在PVC树脂中得以充分分散。
典型的加料顺序如下:
①低速下,将PVC树脂加到混合室中;
②在60℃于高转速下,将稳定剂及皂类加入到树脂中;
③在80℃左右,于高转速下,将加工改性剂、内润滑剂、颜料及抗冲击改性剂加到料中;
④100℃左右,高转速下,加入蜡类;
⑤110℃高转速下加填料;
⑥在110℃~120℃低转速下排出物料,送入转动着的冷混机中;
⑦冷混到40℃排出,过筛使用。
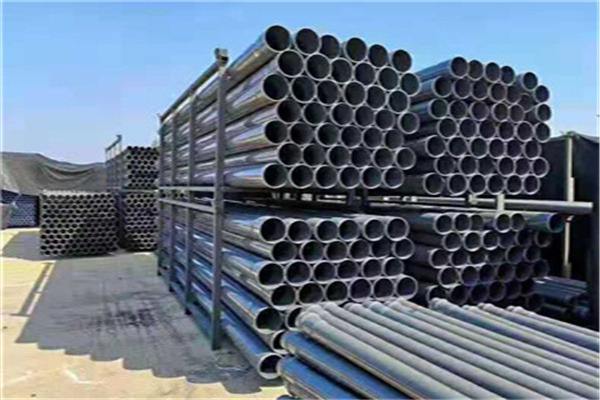